Metal Injection Molding (MIM) and Die Casting are two prominent manufacturing processes that play pivotal roles in producing custom metal parts across various industries.
Both techniques offer distinct advantages and cater to different needs, making them essential components of modern manufacturing.
In this article, we delve into the intricate world of MIM and Die Casting, exploring their unique characteristics, applications, and the factors to consider when choosing between them. Whether you’re aiming for intricate geometries or high-volume production, understanding the differences between MIM and Die Casting is crucial for making informed decisions in your manufacturing endeavors.
Metal Injection Molding (MIM) process
The Metal Injection Molding (MIM) process is a sophisticated manufacturing technique that combines the versatility of plastic injection molding with the strength and durability of metal components. It begins with the formulation of a feedstock, which consists of fine metal powders mixed with a binder material. This feedstock is then injected into a mold cavity under high pressure, allowing it to take on the desired shape.
After injection, the molded parts undergo a debinding process to remove the binder material, leaving behind a “green” part composed of metal powder. These green parts are then subjected to a sintering process, where they are heated to high temperatures in a controlled atmosphere. During sintering, the metal particles fuse together, resulting in a fully dense metal component with the desired mechanical properties.
The MIM offers exceptional design flexibility, allowing for the production of complex geometries and intricate features that would be difficult or impossible to achieve with traditional manufacturing methods. Additionally, MIM enables the use of a wide range of metal alloys, including stainless steel, titanium, and tungsten, offering versatility in material selection to meet specific application requirements.
Overall, the MIM process provides a cost-effective solution for producing high-quality metal components with tight tolerances and excellent mechanical properties, making it an ideal choice for a wide range of industries, including automotive, aerospace, medical, and consumer electronics.
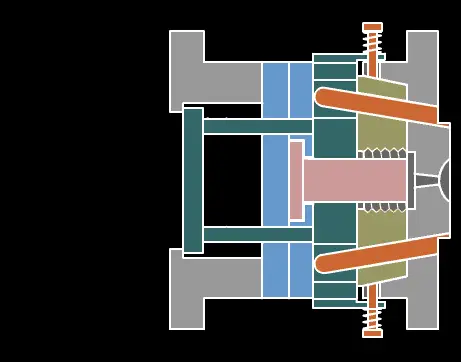
Advantages of MIM
Complex Geometries: MIM allows for the production of intricate and complex shapes with high precision. This includes features such as undercuts, thin walls, and fine details that would be difficult or impossible to achieve with conventional machining or casting methods.
Design Flexibility: MIM offers unparalleled design flexibility, enabling engineers to create parts with tailored properties to meet specific application requirements. This includes the ability to incorporate multiple features into a single component, reducing the need for assembly and improving overall efficiency.
Cost-Effectiveness: While the initial tooling costs for MIM can be higher than other manufacturing methods, the ability to produce complex parts in high volumes can result in significant cost savings over time. Additionally, MIM reduces material waste and secondary machining operations, further lowering production costs.
Excellent Surface Finish: MIM parts typically exhibit a smooth surface finish straight from the molding process, reducing the need for additional finishing operations. This not only improves aesthetics but also ensures consistent performance and functionality.
Overall, the advantages of MIM make it a preferred choice for producing high-precision, complex metal components for a wide range of industries, including automotive, aerospace, medical devices, and consumer electronics.
Material Versatility: MIM supports a wide range of materials, including stainless steel, titanium, copper alloys, and more. This versatility allows manufacturers to choose the optimal material for each application, balancing factors such as strength, corrosion resistance, and thermal conductivity.
Limitations of MIM
While Metal Injection Molding (MIM) offers numerous advantages, it also has some limitations that should be considered:
Initial Costs: The upfront investment required for tooling and equipment in MIM can be significant compared to traditional manufacturing methods. This may pose a barrier to entry for smaller businesses or projects with limited budgets.
Longer Lead Times: The MIM process typically involves multiple steps, including tooling design, material preparation, injection molding, debinding, and sintering. As a result, the lead times for MIM-produced parts can be longer compared to simpler manufacturing processes.
Size Constraints: MIM is best suited for producing small to medium-sized parts with complex geometries. Larger parts may be challenging to manufacture using MIM due to limitations in mold size and handling during the debinding and sintering stages.
Overall, while MIM offers numerous benefits for producing complex metal components, it is essential to consider these limitations and assess whether they align with the specific requirements of your project. Working with experienced MIM manufacturers can help mitigate these challenges and optimize the production process for your needs.

Explanation of the die casting process
Die casting is a metal casting process that involves forcing molten metal into a mold cavity under high pressure. The molten metal is typically injected into the mold cavity at high speed using a plunger or piston. Once the metal solidifies, the mold is opened, and the casting is ejected.
The die casting process can be categorized into two main types: cold chamber die casting and hot chamber die casting. In cold chamber die casting, the molten metal is ladled into a cold chamber before being injected into the mold cavity, while in hot chamber die casting, the molten metal is kept in a heated chamber connected directly to the mold cavity.
Die casting molds, also known as dies, are typically made from hardened tool steel and consist of two halves: the cover die (or ejector die) and the ejector die (or moving die). These dies are precision-machined to the desired shape and are designed to withstand the high pressure and temperature of the molten metal during the casting process.
Die casting offers several advantages, including high dimensional accuracy, excellent surface finish, and the ability to produce complex shapes with tight tolerances. It is suitable for high-volume production of parts with consistent quality and is commonly used in industries such as automotive, aerospace, consumer electronics, and appliances.

Advantages of die casting
High production efficiency: Die casting allows for the rapid production of large volumes of parts. The process is highly automated, with short cycle times, making it ideal for mass production.
Excellent dimensional accuracy: Die casting molds are precision-machined to the desired specifications, resulting in parts with tight tolerances and consistent dimensions. This level of accuracy is crucial for parts that require precise fit and function.
Superior surface finish: Die casting produces parts with smooth surfaces and fine details, often eliminating the need for additional finishing processes. This results in parts with a high-quality finish straight out of the mold.
Strength and durability: Die-cast parts are known for their excellent mechanical properties, including high strength and durability. This makes them suitable for applications that require robust and reliable components.
Complex geometries: Die casting allows for the production of parts with intricate and complex geometries that may be difficult or impossible to achieve using other manufacturing processes. This versatility opens up new design possibilities for engineers and designers
Limitations of die casting
Despite its many advantages, die casting also has some limitations that should be considered:
- High initial tooling costs: The cost of designing and manufacturing the die casting mold can be significant, especially for complex parts with intricate geometries. This initial investment may be prohibitive for some small-scale or low-volume production runs.
- Limited material options: While die casting can accommodate a variety of materials, the selection is more limited compared to other manufacturing processes like metal injection molding (MIM). Certain materials may not be well-suited for die casting due to their properties or processing requirements.
- Design constraints: Die casting imposes certain design constraints, such as draft angles, uniform wall thickness, and avoiding sharp corners, to ensure successful mold filling and part ejection. These limitations may restrict the design freedom for some parts.
- Porosity and shrinkage defects: Die casting can be prone to defects such as porosity and shrinkage, especially in thicker sections of the part. These defects can affect the mechanical properties and surface finish of the final product and may require additional processing to rectify.
- Limited size and weight range: Die casting is best suited for medium to large-sized parts, typically ranging from a few grams to several kilograms. Producing very small or very large parts may be challenging or impractical using die casting methods.
- Longer lead times: The design, manufacturing, and testing of die casting molds can take time, resulting in longer lead times compared to other manufacturing processes. This may impact the overall production schedule and time-to-market for new products.
Comparison between MIM and Die Casting
When comparing Metal Injection Molding (MIM) and Die Casting, one of the key factors to consider is cost. Here’s a comparison of cost considerations between the two processes:
Initial Tooling Cost:
The initial tooling cost for MIM is generally lower compared to die casting.
The mold cost includes the price of the mold as well as the cost of maintenance and replacement. The original price of the mold depends on the complexity of the mold, which is directly related to the complexity of the part. Therefore, the cost should be related to the complexity of the part. Since a set of powder metallurgy molds often produces a large number of parts, the mold material should be able to withstand high pressure and powder friction
Production Cost:
MIM: The production cost for MIM parts can vary depending on factors such as part complexity, material selection, and production volume. While MIM offers cost advantages for complex parts with lower production volumes, it may be less cost-effective for high-volume production runs.
Die Casting: Die casting generally offers lower production costs compared to MIM for high-volume production runs. Die casting is a highly efficient process that can produce large quantities of parts at a lower cost per unit.
Material Selection:
The die casting process is used for materials with low melting points and good fluidity, such as aluminum and zinc alloys. Products made using this process have limited strength, wear resistance, and corrosion resistance due to material constraints. The MIM process can handle a wider range of raw materials.
Material Cost:
MIM: The cost of materials for MIM parts includes the cost of metal powders and binder materials. The material cost per part is influenced by factors such as part volume, density, and material composition.
Die Casting: The material cost for die casting includes the cost of molten metal used to fill the molds. The material cost per part is determined by factors such as part volume, material composition, and material wastage during the casting process.
Secondary Processing Cost:
MIM: Additional secondary processing steps such as debinding, sintering, and finishing may incur additional costs for MIM parts.
Die Casting: Die casting parts may require secondary processing steps such as machining, surface finishing, and heat treatment, which can add to the overall production cost.
Overall Cost Efficiency:
The overall cost efficiency of MIM vs. die casting depends on factors such as part complexity, production volume, material requirements, and quality considerations. While MIM may offer cost advantages for complex parts with lower production volumes, die casting is generally more cost-effective for high-volume production runs of simpler parts.
In summary, cost considerations play a significant role in deciding between MIM and die casting for manufacturing custom metal parts. Evaluating the initial tooling cost, production cost, material cost, secondary processing cost, and overall cost efficiency can help manufacturers make informed decisions based on their specific requirements and budget constraints.
Conclusion
Choosing the right manufacturing process for custom metal parts is crucial for achieving the desired quality, cost-effectiveness, and design flexibility.
Metal Injection Molding (MIM) and die casting are widely used processes, each with their own advantages and limitations. MIM excels in producing complex geometries and utilizing a variety of materials, while die casting is suitable for producing large parts with high efficiency and excellent dimensional accuracy.
By considering cost, design requirements, material properties, and production volume, you can decide when to choose the most suitable process for your custom metal parts.
Choose a professional MIM supplier
We have the capability for independent material feedstock development, allowing us to customize and optimize alloy formulations according to customer requirements
With nearly 20 years of production experience, we have continuously refined our process and improved production efficiency, ensuring product quality and timely delivery.
Our dedicated team of engineers, technicians, and quality control experts provides comprehensive technical support and service to our customers, ensuring smooth production processes and meeting customer needs.
To learn more about MIM technology and our manufacturing services, please don’t hesitate to contact us. Whether you need customized parts, technical consultation, or a quotation, our professional team is ready to support you. Reach out to us today to discuss your project requirements and find the best solution together.